Case Study: Clow Valve
Company Background:
Manufactures and distributes a variety of Water valves, Hydrants and Pipe, for residential housing and industrial development projects within state and local municipalities.
Challenge:
Clow Valve launched an aggressive initiative to optimize the process of manufacturing valve bodies. The objective was to design a system that would allow for uninterrupted flow and unattended processing of the valve body from receipt of raw casting to presentation at the powder coating process in preparation for assembly. This would require comprehensive reevaluation of equipment platforms and conventional manufacturing methods.
Assessment:
The existing process consisted of multiple interrupted operations, each proceeded by lengthy set ups and accompanied by labor-intensive material verification and cumbersome conveyance activities using overhead cranes or load assist equipment. These were necessitated by limitation of the current technology platforms to efficiently process the full feature and weight range of the valve body part family, which can reach 300lbs with outside box dimensions of 20” high, 20” long, and 20” deep, and require complex multi-side machining of the valve body end.
Solution:
Acieta designed a flexible machining cell consisting of 3 Horizontal Machining Centers, 1 Vertical Machining Center, a 6-Axis Robot with a Weight Capacity of 880 lbs. on a 60’ Track with Double Grippers, Cell Controller, and Vision systems for part orientation on all conveyors. Engineering studies supported configuration of robot activity internal to machine cycle times and allow it to sustain throughput requirements of all machines in the cell with maximum process efficiency.
End Result:
The system, which has now produced in excess of 1,000,000 valve bodies at a rate of 600-700 per day, allows for uninterrupted processing of valve bodies from palletized receipt of the raw casting to delivery by conveyor of the machined valve body to powder coat in preparation for final assembly of the completed valve. One attendant manages all cell requirements including tooling, changeover, and alarm response.
To discuss known AUTOMATION OPPORTUNITIES or discover new ones:
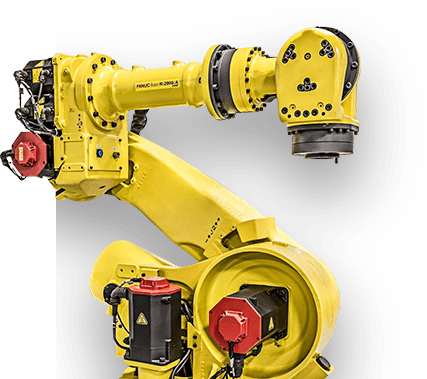