Case Study: Axle Shaft
Company Background:
For close to a century, the company has been influencing positive change on every continent. With sales in 2011 exceeding $60 billion, it is the world’s leading manufacturer of construction and mining equipment, diesel and natural gas engines, industrial gas turbines and diesel-electric locomotives.
Challenge:
Growth in production demand drove the company to expand their North American manufacturing capacities for the axles and axle shafts in large mining trucks. To meet production demands and ensure a robust process for producing high-quality parts, they required expanding their operations and improving on an existing manufacturing cell and process for producing the axle shafts. Key goals were to increase capacity and improve uptime and performance while delivering a safe and ergonomic work environment for their operators.
Assessment:
The existing facility and manufacturing cell for the axle shafts was developed and integrated more than fifteen years ago using outdated technology and automation equipment that was under-sized, resulting in many inefficiencies. Increases in production demands and the addition of new shaft products exceeded the capabilities of the existing axle shaft manufacturing cell. Years of running production on the existing manufacturing cell identified a number of inefficiencies and design flaws in the equipment and process that was driving increased cost into the manufacturing of the axle shafts.
Solution:
Our experienced team of engineers team developed a manufacturing process that consisted of a raw shaft, each weighing no more than 800 lbs., being transferred into the automation process via an inbound conveyor, capable of holding up to 16 shafts. The FANUC Robotics M900iA/600 robot then transports the shaft through the lathe horizontally before traveling to the part marker, spline roller and hardener. The automated process is complete once the robot transfers the axle shaft through the temperature furnace, straightener, buffer, and finally to the queuing rack where it will be placed in an outbound cooling conveyor system.
End Result:
In summary, the robotic automation cell that Acieta designed helped to increase production as well as create a process for producing high-quality goods. The safe and ergonomic workflow demands were met with improving the uptime of the process as well as improving upon the previous methods.
To discuss known AUTOMATION OPPORTUNITIES or discover new ones:
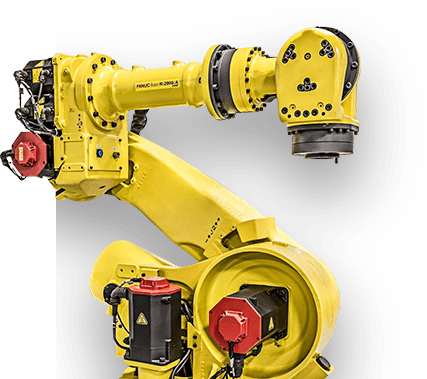