Maximize Efficiency and Productivity
Pick, Pack, and Palletizing Solutions by Acieta

Custom Robotic Palletizing Solutions — Designed to Deliver Results
Our robotic palletizing solutions help manufacturers increase throughput, reduce labor costs, and improve safety—all while ensuring consistent quality. By automating your end-of-line processes, you can meet higher demand, lower operational risks, and free your team to focus on what matters most.
With over 100 years of combined experience and more than 10,000 systems installed worldwide, we have the expertise to deliver customized solutions that support your goals. Our team works with you throughout the process, ensuring systems integrate smoothly with your existing operations and data tracking methods.
Because we specialize in custom palletizing systems, you will get a solution designed around your operations. These systems can integrate smoothly with your WMS or MES for comprehensive production monitoring, often achieving 85%+ OEE. Key use cases and components from past projects include:
|
|
|
|
|
|
|
|
|
|
|
|
Discover how we integrate fully automated pallet conveyor systems, bag palletizing robots, case palletizers, robotic case packers and other advanced palletizing solutions to optimize your operations.
Looking for something specific? We’re ready to collaborate with you to find the perfect solution for your facility. Contact us today to start the conversation.
Ready to Streamline End-of-Line Production? Contact Us Today!
Find the right robotic palletizing solution to meet your operational needs. Whether you’re planning a new project or exploring options, our team of experts is ready to provide tailored recommendations. Fill out the form and let’s start the conversation.
To discuss known AUTOMATION OPPORTUNITIES or discover new ones:
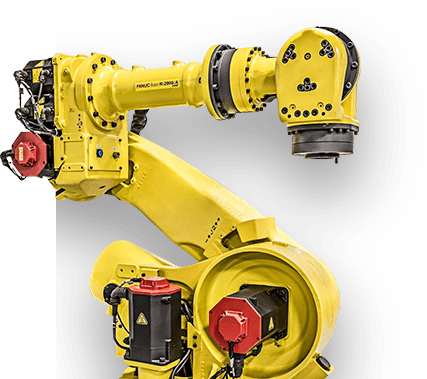